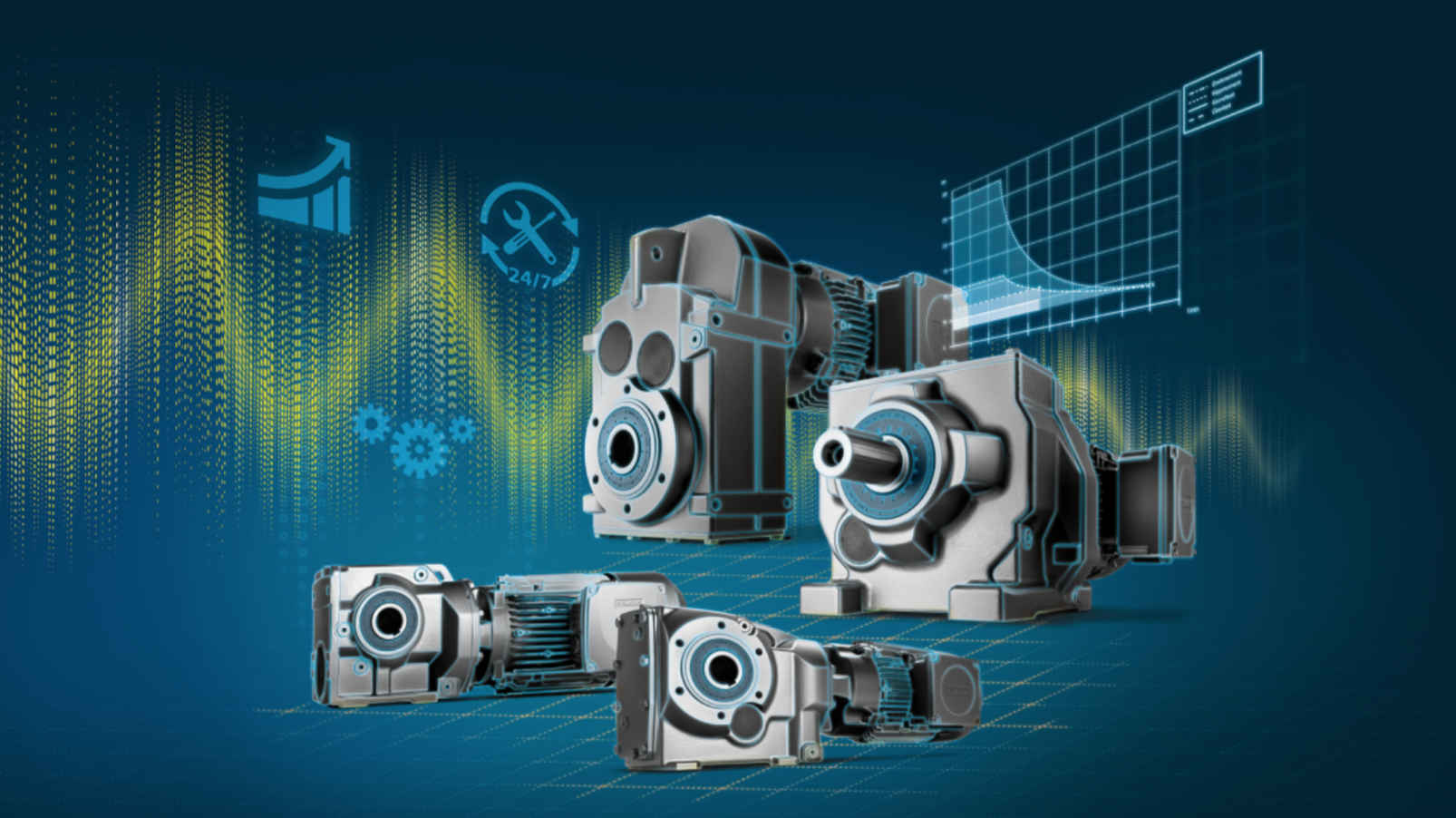
The first step to wiring an AC gear motor is to understand the layout of the intended AC gear motor design. The article seeks to narrate the necessary information needed to get you comfortable with handling an AC gear motor together with other attached necessities.
Generally, for the AC torque motors to gain low speeds, they will need to increase the pole logarithm and adopt the cage rotor structures. Their primary mode of operation is on a low-speed state and with a high load. Their operational flexibility also allows them to operate on a stalled state on a long term or short term basis. Such a work environment enables the motors to provide the load with both the brake torque/reverse torque and the stable torque. The torque motors’ shaft power output is on the basis of constant torque provision and not the steady power supply.
The gearbox or speed reducer component consists of a gear-worm drive, a worm drive, and a gear drive. The component’s constituents are under a designed rigid housing enclosing. The gearbox is functionally applicable as a gearing mechanism for the working machine and the driving link. The speed reducer earned its place in modern machinery due to the role it plays to match the transmission torque and the revolution speed between the actuator/work machine and the driving machine.
The composition of an ATO AC gear motor constitutes of a gearbox and a single-phase AC torque motor. Its characteristic description empowers it with a high slopping and starting torque portfolio. Thus it only takes changing the power supply voltage to control the speed of the motor. The provision of the unique rotor is an excellent performer for tension-based, winding, and holding applications.
Table of Contents
AC Torque Motors Specifications
Before we initiate the testing phase of the AC torque motor with gearbox, we first need to highlight the torque motor specifications that will be relevant during the testing phase. They are as follows:
- 6W Rated Power
- 50 Hz frequency
- 220V AC Rated Voltage
- 1250 rpm Rated Speed
- A 15:1 Gear Ratio of the Gearbox
- An availed 0.8μF Capacitor upon the purchase of the 6W Gear Motor
The electrical design and wiring of a gearbox constitute of three electrical wires. They are a white wire, a blue wire, and a red wire. The white wire and the blue wire connect to the capacitor. The motor’s rotational direction is determinant of a supplied 250V 15A powered switch. Thus it is advisable to make use of a circuit diagram to produce an ideal wiring outcome.
Wiring Procedure
- Use the blue and white wires’ ends to connect the capacitor. Make use of the white wire to make a connection that leads to the transfer switch.
- The power supply should connect to the intermediate terminal leading to the transfer switch.
- The final step is to connect the power code, and you are through with the wiring phase.
Power on and Testing
- If you toggle the switch on a counterclockwise direction, the rotation of the motor should adhere towards the clockwise direction.
- If you toggle the switch on a clockwise direction, the rotation of the motor should adhere towards the counterclockwise direction.
The gearing configuration applicable to the AC gear motor is either right-angle or in-line. The lower backlash of the in-line modification is responsible for enhanced positioning accuracy and added efficiency in the speed-to-torque conversion. They form one line through an alignment between the output shaft and the motor shaft, thus their specific feature. The reducers applicable in the right-angle configuration are however typically more expensive than the in-line reduction gears. Still, feel like you studying rocket science? Read more on AC motors to reduce the fever.
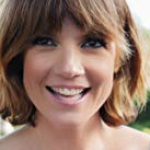